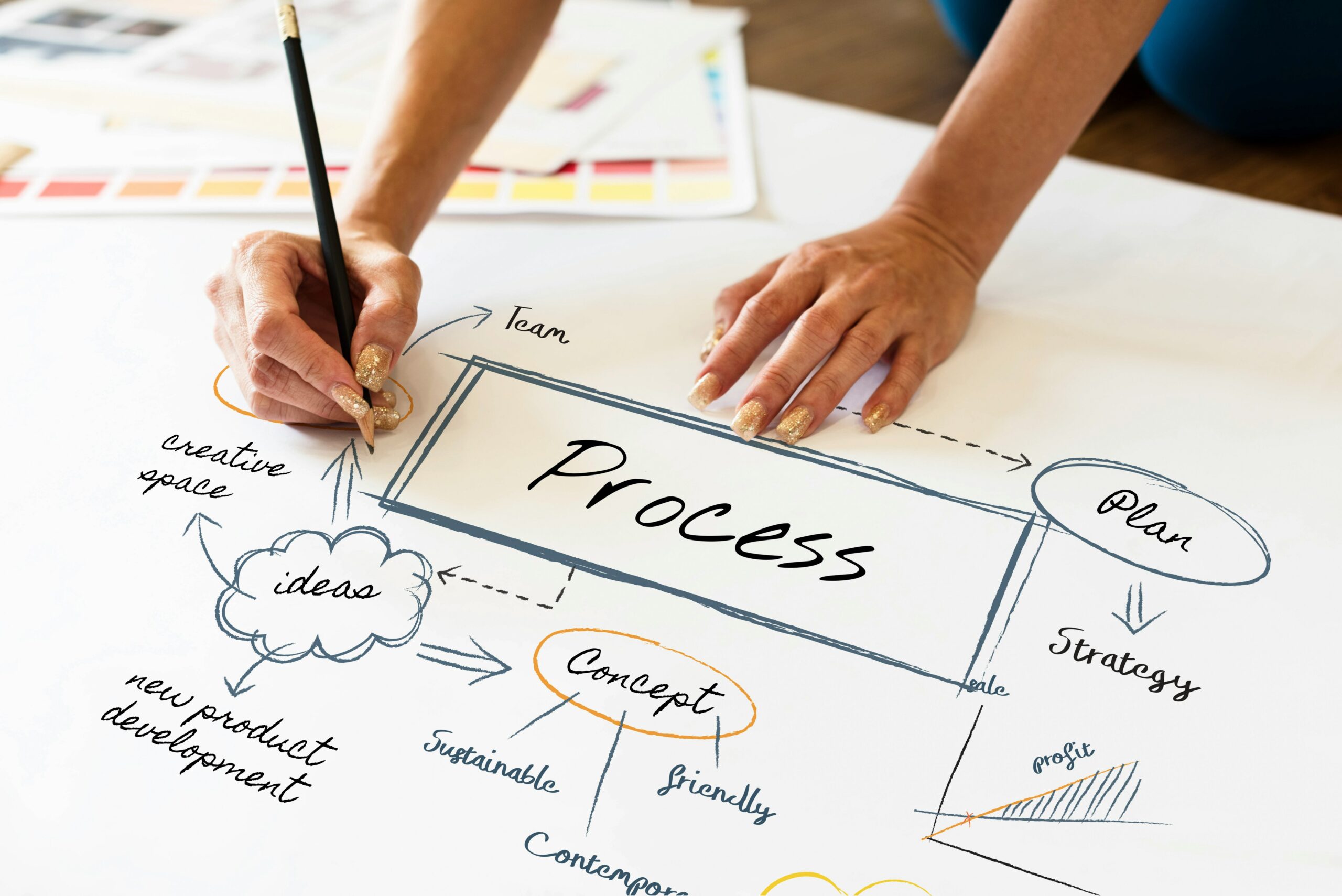
In every organization—whether a small startup, a government agency, or a multinational corporation—processes are the engines that drive day-to-day operations. These processes, from manufacturing and logistics to customer service and administration, must work efficiently to support quality outcomes and profitability. Over time, however, even the most well-designed systems can become outdated, slow, or redundant. That’s where process improvement methods come in.
Process improvement is a structured approach to identifying inefficiencies, eliminating waste, and optimizing workflow. It’s not just about cutting costs or speeding up delivery—it’s about creating smarter, leaner, and more adaptive systems that can grow with the organization. Whether improving customer satisfaction, boosting employee productivity, or increasing output, these methods provide a blueprint for sustainable operational excellence.
Why Process Improvement Matters
Organizations that continually assess and improve their processes gain a competitive advantage. They’re more agile, better at adapting to change, and more responsive to customer needs. On the other hand, businesses that ignore inefficient processes risk higher costs, lower morale, quality issues, and customer dissatisfaction.
Process improvement enhances transparency and accountability by documenting workflows and performance metrics. It also fosters a culture of continuous improvement, encouraging employees at every level to look for better ways to do their work.
Most importantly, process improvement leads to measurable outcomes: shorter cycle times, higher quality output, reduced errors, and more satisfied stakeholders. When done right, it transforms complexity into clarity.
Defining Process Improvement Methods
There are several recognized methodologies for process improvement, each offering a distinct framework and set of tools. While the core principle remains the same—identify, analyze, and improve—these methods vary in focus and application. Below are some of the most widely used approaches:
Lean Methodology
Lean is a process improvement method focused on maximizing value while minimizing waste. Originating in manufacturing, it is now applied across healthcare, finance, education, and tech industries.
Lean identifies eight types of waste: defects, overproduction, waiting, non-utilized talent, transportation, inventory, motion, and extra processing. Using tools like value stream mapping, 5S (Sort, Set in order, Shine, Standardize, Sustain), and Kaizen (continuous improvement), Lean helps organizations streamline processes, improve flow, and empower employees.
Lean’s strength lies in its simplicity and focus on delivering what customers truly value.
Six Sigma
Six Sigma is a data-driven methodology that reduces process variation and defects. It uses the DMAIC framework: Define, Measure, Analyze, Improve, and Control. Six Sigma emphasizes precision and control, making it ideal for environments where consistency and accuracy are critical.
In Six Sigma, statistical analysis plays a central role. Teams use tools like control charts, root cause analysis, and failure mode and effects analysis (FMEA) to uncover process issues and develop long-term solutions.
Six Sigma certifications—such as Yellow Belt, Green Belt, and Black Belt—equip professionals with the skills to lead improvement initiatives within their organizations.
Lean Six Sigma
Lean Six Sigma combines the best of Lean and Six Sigma to drive speed and quality simultaneously. This hybrid approach balances Lean’s customer-focused, waste-eliminating principles with Six Sigma’s rigorous, data-centric problem-solving.
Lean Six Sigma is especially popular in larger organizations that require quick wins and profound systemic change. It offers a versatile toolkit and a powerful strategy for optimizing departmental performance.
Total Quality Management (TQM)
Total Quality Management is a holistic approach that integrates quality into every aspect of an organization. It emphasizes long-term success through customer satisfaction, continuous improvement, and employee involvement.
TQM encourages cross-functional collaboration and leadership commitment to quality. It includes tools such as benchmarking, statistical process control, and the Plan-Do-Check-Act (PDCA) cycle.
Rather than focusing on isolated improvements, TQM fosters an organizational culture where quality is everyone’s responsibility.
Business Process Reengineering (BPR)
While most methods focus on incremental improvement, Business Process Reengineering takes a radical approach. BPR involves rethinking and redesigning entire processes from the ground up to achieve dramatic gains in productivity, efficiency, or customer service.
BPR is suitable for organizations facing significant challenges or undergoing digital transformation. Though riskier than gradual methods, BPR can lead to revolutionary breakthroughs when executed with strong leadership and clear goals.
Steps to Implement Process Improvement Successfully
Regardless of the method used, a few core steps are essential for successful process improvement:
Identify the Process to Improve
Begin by selecting a high-impact or problematic process. This could be a production bottleneck, a customer complaint area, or a repetitive task that consumes excessive time or resources.
Map the Current Process
Visualize the process using tools like flowcharts or value stream maps. This helps identify where delays, redundancies, or inefficiencies exist.
Gather Data and Analyze
Collect data on performance metrics such as time, cost, error rates, or satisfaction levels. Analyze root causes of inefficiency using methods like the 5 Whys or fishbone diagrams.
Design the Improved Process
Based on your findings, redesign the process to eliminate waste, reduce errors, and improve output. Consider automation, role adjustments, or policy changes as needed.
Implement and Monitor
Roll out the improved process, providing training and support to stakeholders. Monitor performance to ensure the changes are producing desired results.
Standardize and Sustain
Document the new process, update SOPs (Standard Operating Procedures), and integrate feedback loops to sustain improvements over time.
Building a Culture of Continuous Improvement
One-time fixes won’t deliver lasting value. The most successful organizations embed process improvement into their culture. This means encouraging curiosity, rewarding innovation, and making it safe to question existing systems.
Leadership plays a vital role in modeling this mindset. When leaders show commitment to ongoing learning and improvement, it signals to teams that positive change is not just permitted—it’s expected.
Employee involvement is equally critical. Frontline workers often have the most profound insights into process inefficiencies. Creating opportunities for staff to suggest improvements and participate in change initiatives promotes ownership and morale.
Regular reviews, performance dashboards, and improvement workshops help sustain momentum and prevent regression into old habits.
Leveraging Technology in Process Improvement
Digital tools can improve the process by enhancing visibility, automation, and data analysis. Workflow management software, robotic process automation (RPA), and analytics dashboards allow organizations to track performance and adapt quickly.
Cloud-based collaboration tools also facilitate real-time input from teams across departments or locations. AI-powered solutions can even predict bottlenecks or suggest optimizations before problems arise.
However, technology is only as effective as the strategy behind it. It should support—not replace—a thoughtful, human-centered approach to improvement.
Achieving operational excellence is not a destination—it’s a journey paved with insight, action, and adaptability. By embracing process improvement methods, organizations can evolve purposefully, enhance customer satisfaction, and strengthen their internal culture.
Whether through Lean’s focus on value, Six Sigma’s data-driven rigor, or TQM’s quality-first ethos, the path to better processes begins with a commitment to change. In an ever-shifting world, those who continuously refine how they work will not only survive—they will lead.